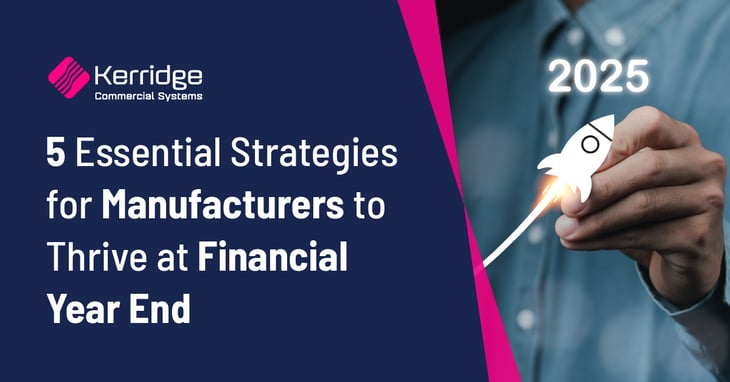
For many businesses across South Africa, the financial year end is in sight. Manufacturers have a prime opportunity to assess operations, enhance efficiency, and set the stage for future success. Focusing on industry-specific practices during this period can lead to significant improvements.
Herewith 5 essential strategies to improve your manufacturing operations:
1. Comprehensive inventory reconciliation for manufacturers
Accurate inventory management is vital for manufacturers. However, a thorough year-end reconciliation involves many processes, which can be complex and time-consuming. Utilising specialised inventory management software can streamline this process, which provides real-time data and reduces manual effort (along with a host of other benefits).
- Physical inventory count: Use digital technologies to conduct detailed counts to ensure records match actual stock levels.
- Identifying discrepancies: Investigating variances to uncover issues such as shrinkage, misplacements or recording errors.
- Process analysing: Analysing discrepancies to improve inventory control systems and reduce future errors.
2. Balance sheet reconciliations for manufacturers
The accuracy of financial statements is vital for the success of any manufacturing business. To ensure this, it is essential to follow steps that provide reliability and transparency in financial reporting.
- Account verification: Reconciling all balance sheet accounts, including assets, liabilities and equity, to confirm their accuracy.
- Supporting documentation: Maintaining detailed records to substantiate account balances, as well as facilitating internal reviews and external audits
3. Evaluation of your manufacturing business' production processes
The end of the year presents a valuable opportunity to assess and enhance the workflows within your manufacturing operations. By focusing on continuous improvement initiatives, you can boost productivity and achieve meaningful cost savings.
- Process analysis: Reviewing production stages to identify bottlenecks or inefficiencies.
- Quality control: Assessing defect rates and implementing measures to enhance product quality.
- Lean manufacturing: Applying lean principles minimises underutilisation.
4. Assessment of supplier and vendor relationships for manufacturers
Robust supplier partnerships are vital for ensuring seamless manufacturing operations, as they foster collaboration, enhance production efficiency, and contribute to the overall success of the supply chain.
- Performance review: Evaluating suppliers based on delivery timeliness, quality, and cost-effectiveness.
- Contract analysis: Reviewing terms to ensure they align with current business needs and market conditions.
- Diversification: Considering alternative suppliers to mitigate risks associated with supply chain disruptions.
5. Strategic financial planning for manufacturers
Planning for the future is critical which is why proactive financial planning sets manufacturers up for sustainable growth. Actions that can help your planning include:
- Budget development: Creating detailed budgets that reflect anticipated expenses and revenues.
- Capital investment: Prioritising investments in technology, equipment, or process improvements that offer the highest returns.
- Risk management: Identifying potential financial risks and developing strategies to mitigate them.
By focusing on these key areas during your financial year end, manufacturers can enhance operational efficiency, strengthen financial health and position themselves for a prosperous year end. These key objectives no longer need manual intervention or multiple systems to support multiple functions. A good MRP can do this for you.
Ready to supercharge your manufacturing operations? Ask us how. Our MRP solution is developed with Manufacturers in mind.